Static electricity is a natural phenomenon, which can be generated from different ways, such as contact, friction, stripping and so on. Electrostatic protection technologies, adopted by electronics, semiconductors, petroleum, ordnance, textile, rubber, aviation and military fields, resort to reduce the loss caused by static electricity.
- Precautionary Measures
- Grounding
- Shield
- Neutralization
- Protective Equipment
- Daily Life Common Sense
- Explanation on Electrostatic
- Main ESD Prevention Products
- Electrostatic system
Precautionary Measures
There are three main anti-static measures: antistatic clothing, antistatic shoes and anti-static wrist bands.
Anti static shoes and anti-static wrist bands are used to conduct static electricity so as to avoid accumulation on the human body.
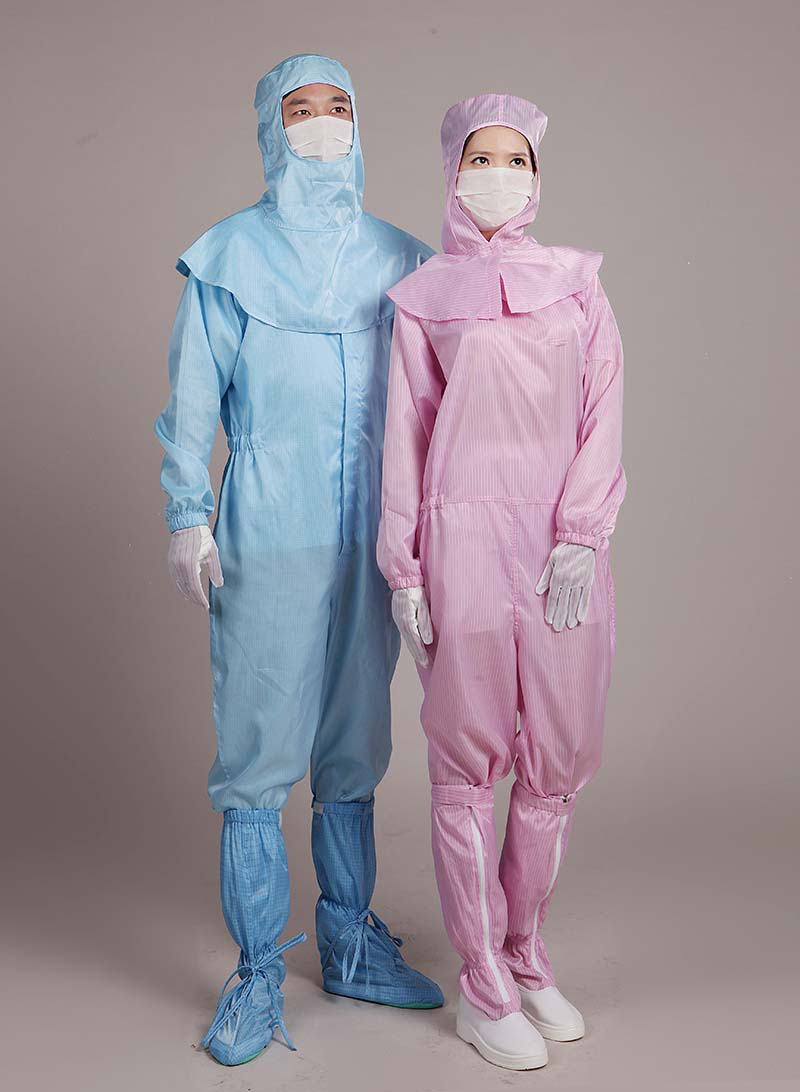
Common clothes produce a large static voltage (> 1000V) while the wearer moving around. This wouldn’t occur to antistatic clothes, and that’s the main reason for wearing antistatic clothes.
Long strip material anti-static clothing can not shield the static electricity generated by clothing (still >1000V after wearing). While he grid material antistatic clothing can do its job (<200V).
The static electricity is introduced into the outer ground line of the factory through conductive floor boards and the ground wires .
The prevention includes preventing static electricity generation and preventing its damage.
Electrostatic protection is a long-term system engineering, any fault or carelessness will lead to the failure of electrostatic protection.
Mainly the measures for electrostatic protection in the production process are electrostatic leakage, dissipation, neutralization, humidification, shielding and grounding.
Human body electrostatic protection system usually consists of anti-static wristband, anklet, work clothes, shoes & socks, caps, gloves or fingerstalls etc., with electrostatic leakage, neutralization and shielding functions.
The ground anti-static treatments are anti-static ceramic steel-based composite movable floor, anti-static steel movable floor, anti-static ceramic floor tiles and so on.
Grounding
Grounding is very important to reduce the electrostatic charge on the conductor, the human body is a conductor, also a main source of electrostatic generation. Therefore, we must reduce the static charge generated by contact with the sensitive electrostatic components. Prevention of static electricity on the human body is best through grounding.
Some grounding devices:
In industry, wristband is the most commonly used grounding device. The wristband will safely and effectively drain the static charge from your body. Reasonable use of a wristband requires reasonable contact with the skin. A dirty or loose wrist strap may retain the static charge, which makes the antistatic control will fail. Conductive footwear or foot grounding can be used to overcome shortcomings of wrist bands.
Work Station Grounding Device
Conductive or electrostatic dissipative working surfaces are an indispensable part of an electrostatic safety workstation, especially where manual assembly occurs. While using wristbands, it is necessary for a clean working surface to be grounded properly at a joint. Conductive or electrostatic dissipative materials can produce electrostatic charges, however., when they are properly grounded, they can effectively drain static charges.
Shield
The next concept is to isolate parts and components during storage or transportation. It is isolated from a charged object or a charged electrostatic field. Insulator is the best way to prevent electrostatic discharge during storage or transportation. Since grounding cannot remove static charges or insulators, it is necessary to isolate sensitive parts and components from them. Reducing conventional plastics and other types of insulators in stationary working, shipping and handling areas is the best way to isolate products from insulators. Isolation can also be done by limiting access to the entire work area or workstation. Finally, we take advantage of the fact that electrostatic charges cannot enter containers made of conductive materials or layers. This effect is called the Faraday cup effect. When storing and transporting electronic components or loading circuit boards, ensure that containers with similar Faraday cup characteristics are used, and these containers will be isolated from electrostatic injuries.
Neutralization
Utilizing electrostatic elimination equipment, its main component is ion generator.
Neutralization is important because earthing and isolation will not release charge from insulators such as synthetic fabrics or conventional plastics. Neutralizing or removing the charge generated in insulator is called ionization. Ions are simply charged substances existing in the air. Ions are produced by natural energy materials. Including sunlight, lighting, open-air flame and radiation. We can get trillions of ions through ion generators, which use high voltages to produce a balanced mixture of charged ions, and fans to help ions drift to objects or regions to neutralize. Ionization can neutralize static charges on insulators in eight seconds, thus reducing their potential damage. Ionization is not a substitute for grounding or isolation. It only reduces the possibility or risk of electrostatic discharge accidents.
Protective Equipment
Personal static eliminator mainly refers to contact static eliminator and auto-sensor static eliminator.
Contact static eliminator
Contact hand-held personal electrostatic eliminator is a device that eliminates static electricity on human body or metal objects by touching metal objects with hand-held devices. But this is only temporary. In daily life, static electricity is produced all the time. After using contact static eliminator for a period of time, our body will feel electric shock when it contacts the electrostatic object/metal conductor again. So when we use the product, we need finish to the work as soon as possible.
Auto-sensor static eliminator
Automatic personal static eliminator is a device that automatically detects the static electricity in the surroundings and then automatically eliminates the static electricity. We don’t need any operation. The most outstanding feature of this automatic key chain is its exquisite workmanship, anti-static load up to 40,000 volts, and the ability to eliminate static electricity continuously.
Daily Life Common Sense
In daily life, people often accumulate static electricity due to clothing, climate, friction and other reasons. When they bump into metal, people will suffer from electric shock pain. Psychological pressure may be caused in some cases. If you avoid touching iron for a while, you may accumulate more electric charges on your body, sooner or later you will suffer from stronger electric shocks.
1. In the house, the rubbing of carpet and sole may produce static electricity, and outside, you may also be electrified by wind. Be careful when you enter or exit metal gate, your hands may experience shock. If this happens repeatedly, the following measures can be taken to avoid electric shock:
1.Don’t touch an iron door directly with your hands. Instead, hold the keys before that(usually you can avoid electric shock), touch the metal with the tip of a key, the electricity on your body will be released and you won’t get shocked.
Principle: Pain caused by hand discharge is due to high voltage discharge, because a sudden contact of your hand and metal door leaves a small area for discharging, resulting in instantaneous high voltage. If you take out the key in your pocket and hold it in a large area (a bunch of keys can’t transfer much electric charge by themselves, so there won’t be an electric shock at this time), then use the tip of a key to contact the large conductor. At this time, the contact point of discharge is not a point on the skin of the hand, but the tip of the key, so the hand will not feel it. (Maybe the key! If it feels pain.)
2. Frequent electric shocks occur when getting off the taxi. The main reason is that static electricity accumulates when the body rubs against the seat when getting off, and when the door closes, the hand will be shocked when it suddenly touches the iron door.
If this often happens, it’s better to take notice when you get off the car, that is, when your body rubs against your seat, you can hold the metal door frame in advance. When static electricity is generated by friction, you can remove static electricity from your body at any time, instead of discharging when you suddenly touch the iron door while getting off.
Explanation on Electrostatic
In order to effectively combat and prevent ESD (electrostatic discharge), the right equipment must be used in the correct way. Because of a series of powerful closed-loop ESD prevention, monitoring and ionizers, ESD can be regarded as a process control problem.
Electrostatic discharge (ESD) is a familiar and underestimated source of circuit board and component damage in electronic assembly. It affects every manufacturer, regardless of its size. Although many people believe they produce products in an ESD-safe environment, in fact, ESD-related damage continues to cost the world’s electronics manufacturing industry billions of dollars a year.
What is ESD?
Electrostatic discharge (ESD) is the sudden flow of electricity between two electrically charged objects caused by contact, an electrical short, or dielectric breakdown. A buildup of static electricity can be caused by tribocharging or by electrostatic induction. The ESD occurs when differently-charged objects are brought close together or when the dielectric between them breaks down, often creating a visible spark. The charge is stable under two conditions.
1. When it “falls” into a conductive but electrically insulated object, such as a metal screwdriver with a plastic handle.
2. When it resides on an insulating surface (e.g. plastic), it can not conduct on it.
However, if an electrically insulated conductor (screwdriver) with sufficient high charge is close to an integrated circuit (IC) with opposite potential, the charge “crossover” causes electrostatic discharge (ESD).
ESD occurs very quickly at very high intensity, usually producing enough heat to melt the internal circuit of semiconductor chips, which seemingly blows out small bullet holes under an electron microscope, causing immediate and irreversible damage. What’s more, a tenth of the cases are so bad that the whole component fails in the final test. In the other 90% cases , ESD damage only causes partial degradation – meaning that the damaged components can pass the final test without detection, and premature on-site failure occurs only after shipment to the customer. It will dishonor a manufacturer to have to correct any manufacturing defects.
However, the main difficulty in controlling ESD is that it is invisible but can damage electronic components. To produce a discharging that can hear a beep, a considerable charge of about 2,000 volts needs to be accumulated, while with 3,000 volts you can sense slight shock and with 5,000 volts you may see sparks.
For example, common components such as complementary metal oxide semiconductor (CMOS) or electrically programmable read-only memory (EPROM) can be destroyed by ESD potential differences of only 250 volts and 100 volts, while more and more sensitive modern components are out there. Including the Pentium processor, it can be destroyed by only 5 volts.
The problem is compounded by activities that cause damage every day. For example, in the vinyl factory floor, there is friction between the floor surface and the shoes. As a result, pure charges accumulate between 3 and 2,000 volts, depending on the relative humidity of the local air.
Even the friction generated by the natural movement of workers on the platform can produce 400~6000 volts. If the worker has treated the insulator during the PCB dismantled or packed in foam box or bubble bag, the net charge accumulated on the workers can reach about 26000 volts.
Therefore, as the main source of ESD hazards, all staff entering the electrostatic protected area (EPA) must be grounded to prevent any charge accumulation, and all surfaces should touch ground to maintain the same potential of everything and prevent ESD from occurring.
Main ESD Prevention Products
The main products used to prevent ESD are wristbands, with curly corduroy and dissipative surfaces or pads – both must be properly grounded. Supplements, such as dissipative footwear or heel straps and suitable clothing, are designed to prevent people from accumulating and maintaining net charges while moving in an electrostatic protection area (EPA).
PCB should also prevent ESD from internal and external transportation during and after assembly. There are many PCB packaging products that can be used in this area, including shielding bags, shipping boxes and mobile trolleys. Although the correct use of these devices will prevent 90% of ESD-related problems, in order to reach the final 10%, another protection is needed: ionization.
The most effective way to neutralize assembly equipment and surfaces that generate electrostatic charges is to use an ionizer, a device that blows ionized air out of the working area to neutralize any charges accumulated on insulating materials.
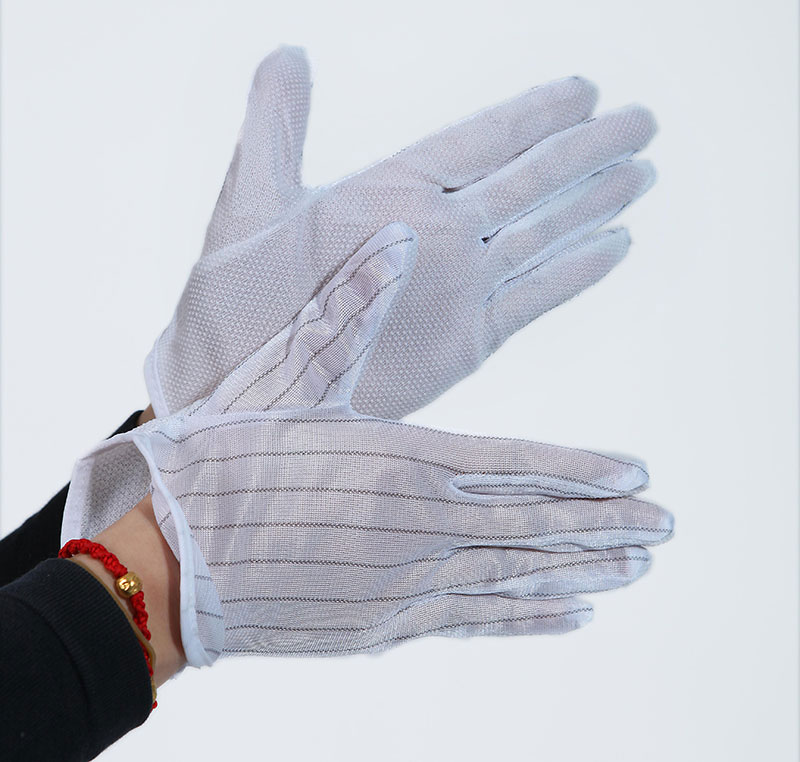
Antistatic Gloves
A common fallacy is that because a bowl belt is attached to the workstation, the charges of insulators in the area, such as polystyrene cups or cardboard boxes, will dissipate safely. By definition, insulators do not conduct electricity, and it is impossible to discharge them in addition to ionization.
If a charged insulator is retained in EPA, it will radiate an electrostatic field, causing a net charge to any nearby object, thus increasing the risk of ESD damage to the product. Although many manufacturers try to prevent insulation materials from their EPA, this method is difficult to implement. Insulating materials are too much part of everyday life – from operators’ comfortable foam mats to plastic covers.
Because of the use of ion generators, manufacturers can accept the fact that some insulating materials appear in their EPA. Since ion generation systems continuously neutralize any charge accumulation that may occur on insulators, they are a reasonable investment for any ESD program.
There are two forms of ion generating equipment in standard electronic assembly:
* Desktop type (single fan)
* Overhead equipment (with a series of fans in a single over top unit).
There are also indoor ion generators, but they are mainly used for cleaning rooms.
To use which one depends on the size of the protected area. Desktop ion generators will cover a single working surface, while overhead ion generators will cover two or three. Another advantage is that the ion generator can also prevent dust from sticking to the product and may degrade the appearance.
However, without proper testing and monitoring of the effectiveness of ESD devices, no protection plan is perfect. First-class ESD control and ionization experts report examples of manufacturers using failed (and therefore useless) ESD devices without knowing their failure.
To prevent this, in addition to standard ESD equipment, ESD vendors also provide a variety of constant monitors, which automatically alarm if a performance exceeds the requirements. The monitor can be used as an independent unit or linked together in the network. It also has an automatic data acquisition network software that displays the performance of operators and workstations in real time.
The monitor can simplify ESD plans by eliminating many routine tasks, such as ensuring proper measurements of bowl belts every day, balancing and correct maintenance of ion generators, and no damage to the worktable grounding points.
Conclusion
The first step in preventing ESD is to correctly evaluate how small details can cause irreparable damage if ignored. An effective plan requires not only the use of effective ESD protection equipment, but also rigorous operating procedures to ensure that all plant personnel are ESD safe.
Although many manufacturers use automatic bowl belt testers, it is common to see operators passing tests or failing because the bowl belt is too loose. Many operators attempt to pass the test by holding the tester close to the wrist with the other hand.
Nonetheless, the good news is that ESD is avoidable. The time and money invested in proper equipment and improved safety procedures will be rewarded by increasing the corresponding eligibility rate.
Electrostatic system
As an effective system for electrostatic protection, it is mainly composed of two parts: hardware and software.
The hardware part includes:
* Body electrostatic protection products
* Anti-static logistics transfer products
* Anti-static floor
* Anti-static operation system
* Anti-static earthing
Anti static grounding must be installed in the anti-static work area.
* Environmental control system
Temperature and humidity control equipment should be installed in the anti-static working area, and environmental cleanliness control system should be installed in the assembly of electrostatic sensitive devices with special requirements, so that the production environment can reach the corresponding cleanliness level.
* Special production assembly equipment
Production equipment such as mounter, Bonding, plug and pull, welding and so on should be adopted.
* Special antistatic products.
* Electrostatic measurement (monitoring) system
The software part includes:
* Training
* Antistatic technology and design documents.
* Professional standards for anti static electricity
* Operation procedures and rules and regulations
* Complete quality assurance system
* Anti-static signs
* Storage and transportation requirements